Vivian Luk
Sun
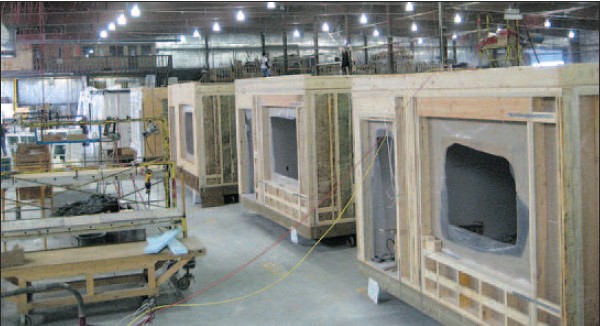
Modular units built at Britco’s factory in Agassiz are shipped to rural communities.

A rendering of the modular housing units that will be built by various contractors under an affordable-housing program.
Modular housing units will be shipped out from local manufacturers to 11 rural communities across B.C. by the end of this month as part of an affordable-housing initiative for seniors, says Minister of Housing and Social Development Rich Coleman.
The units, 358 in all, will be rented out to seniors and people with disabilities in Creston, Pemberton, Port McNeill, Prince Rupert, Qualicum Beach, Keremeos, Lake Country, Lumby, Naramata, New Hazelton and Terrace.
The project costs $15.5 million, and is funded by the provincial and federal government. It is part of the Seniors‘ Rental Housing initiative, a $124-million project that aims to provide affordable housing to seniors.
“We wanted to find a way for seniors to be able to age in their own, small communities,” said Coleman, who inspected one of Britco Structures Inc.’s factories in Agassiz Monday. Britco, one of four modular manufacturers contributing to this project, is building 152 units.
“It’s virtually impossible to build a care home for only five, six people, so they get moved to institutions farther away.
But if we can bring services and home care to them, they wouldn’t have to move.”
The modules will be 600-square-feet, single-storey, one-bedroom houses. The needs of seniors and people with disabilities will be met by wide, lever-handle doors for wheelchair access, lower light switches, showers with sit-down areas and grab-bars in bathrooms.
According to Mike Ridley, executive vice-president of Britco, modular houses are more affordable — $160,000 per unit — because building identical units in a factory assembly line cuts production costs and time. Once the floor, cabinets, windows, kitchen and living room have been completed, the module will be shipped out by truck to a site, where a foundation system, plumbing services and electricity have already been put in place.
“Then you just put it all together like Lego pieces,” Ridley said. “The house will be craned in place. A crew on site will put the sidings and the roof structure on, do some landscaping work and build parking units.”
Rent will either be set at 30 per cent of income, or at a low, flat rate, said Coleman.
All the modules are being built with 100-per-cent B.C. pine-beetle-infected wood that, if unused, would be left to rot.
“Some overseas clients in Japan and China tend to be concerned about the sturdiness of building materials made from infected wood,” said Coleman. “But we’ve performed tests and have proven that pine beetle wood is as good any.”
© Copyright (c) The Vancouver Sun